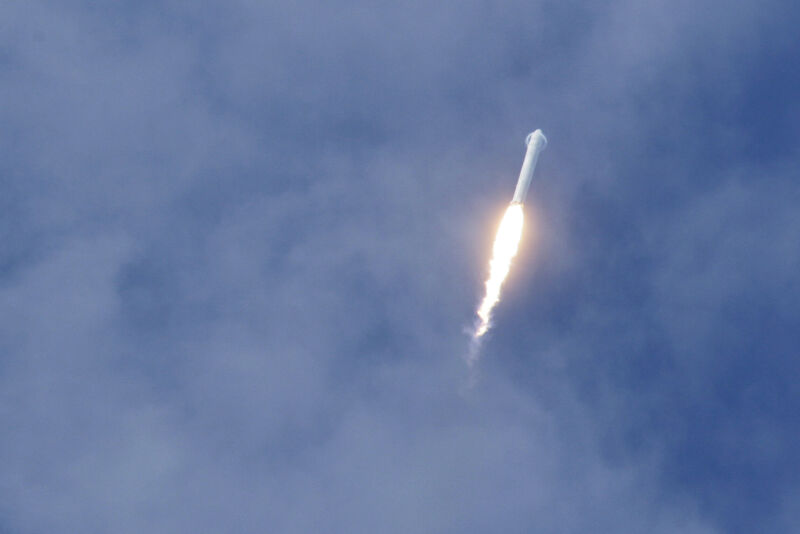
Winds howled across Florida's Space Coast on June 3, 2010, as classic summertime thunderstorms rolled inland off the Atlantic Ocean. The heavens opened up, and torrential rainfall doused some parts of Cape Canaveral with as much as three inches of rain in a single hour.
The storms seemed an ill portent for the very first Falcon 9 rocket, which the SpaceX launch team had moved to the company’s new pad only a day before. After completing a succession of static fire and fueling tests during the spring of 2010, SpaceX finally received approval to launch from the Air Force, with the earliest possible date of June 4.
The stakes were high. In the previous four years, SpaceX had attempted five launches of its much smaller Falcon 1 rocket from a tropical island; three of those launches failed. Now the upstart company had been granted access to America’s most storied spaceport, located on Florida's east coast. Carpeted with high-dollar launch pads and myriad rocket facilities, a failure at Cape Canaveral could damage more than SpaceX’s reputation—it could destroy national security assets.
Four tall lightning towers protected the rocket from strikes during the rains, but post-storm checkouts revealed a weak telemetry signal coming from antennas on the Falcon 9 rocket's second stage. Water from the day’s downpour must have gotten into the electronics. This was a potential showstopper for the next day’s launch attempt; it had to be fixed. To do so, the launch director, Tim Buzza, drove out to the launch pad with the company’s founder, Elon Musk, and a senior director of avionics, Bulent Altan.
They arrived at the launch pad well after dark, and the Falcon 9 rocket had already been lowered from its vertical launch position back into a horizontal configuration.
Altan, who knew the avionics system as well as anyone, climbed a ladder to where the antennas were located on the second stage. He removed a cover to assess the damage, confirming that rain from that day's storms had gotten into the rocket's electronics. Overhead, bright lights shone down. Below, dozens of eyes stared up at Altan.
"I've never felt more exposed than that," he said.
He returned to the ground for a quick huddle with Musk, Buzza, and a handful of other engineers. Should they try and swap out electronics on the pad? Did they need to roll the Falcon 9 back into the company's hangar and delay the launch for a couple of days? No and no. The engineers decided to try a low-tech solution—a blow dryer. Altan went back up the ladder, and he began to wave the dryer back and forth until the antennas and their electronics seemed dry.
Meanwhile, on the ground, Musk and the others restlessly waited. SpaceX was barely eight years old at this point, and the company had survived a near-death experience two years earlier before being saved by NASA funding that had enabled this launch. The Falcon 9 rocket on the pad would fly this test flight, and if all went well, the company could soon begin flying cargo to the International Space Station for NASA. But there were a lot of doubters ready to pounce on SpaceX should it fail. They didn't trust Musk or his company to deliver. Critics didn't like what they viewed as a cowboy attitude toward spaceflight.
And let's be real: here they were, cowboying the night before launch, taking a blow dryer to the rocket.
After he finished, Altan closed the electronics compartment on the rocket and applied silicone sealant so that it would survive its ascent into space. Then, with all eyes on him, he climbed back down to the ground. When Altan stepped off the ladder, Musk walked over with a question.
“You think it is good enough to fly tomorrow?”
“It should do the trick."
Musk did not say anything else right away. He has this stare that he uses on people. It's intense, as if to demand, Is that your final answer? In this case, Musk wanted to know whether Altan was giving his boss the answer he wanted to hear or saying what he really meant. And after several seconds, Musk must have liked what he saw.
"OK," he said.
And it was OK. More than OK, in fact. The next day, although the telemetry signal coming from the second stage antennas still was not quite as strong as hoped for, Musk said they should roll with it anyway. At 2:45pm local time on June 4, 2010, the first Falcon 9 rocket blasted off from the Florida coast.
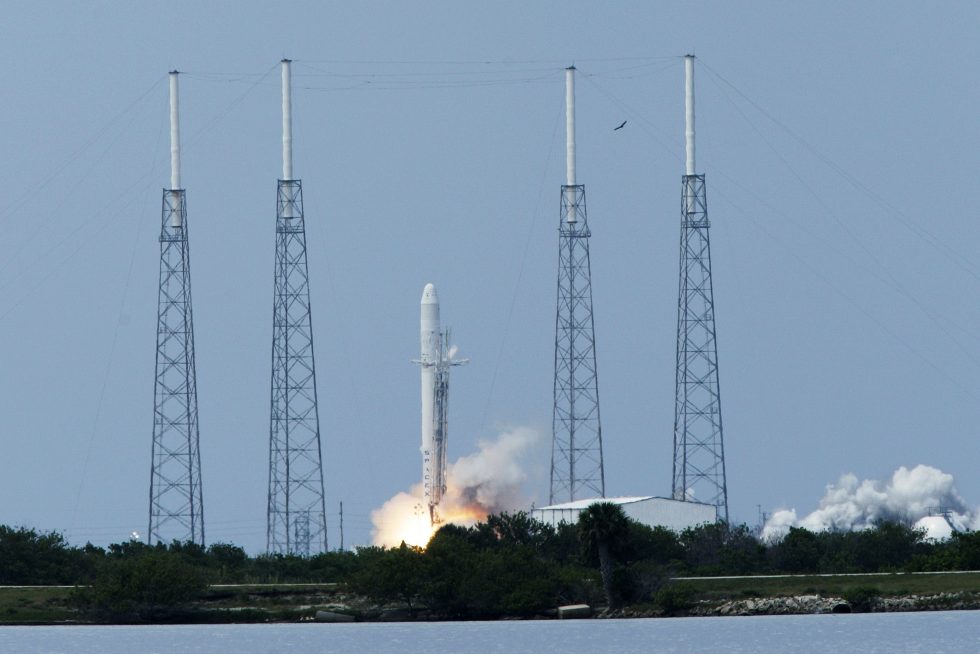
The company’s first goal for the test flight was simple—avoid damaging its launch pad or other valuable facilities at Cape Canaveral. Secondarily, it hoped to reach orbit. It did all of that, and more. With an accuracy remarkable for a brand-new rocket, the second stage inserted itself into orbit at an inclination of 34.494 degrees—just short of its target of 35 degrees.
And so, ten years ago, the Falcon 9 era officially began.
Recapturing commercial launch
This past weekend, SpaceX’s Crew Dragon spacecraft got all of the splashy headlines, and deservedly so for returning humans into space from Florida for the first time since the space shuttle’s retirement nine years ago. But the real workhorse behind the rise of SpaceX over the last decade is undoubtedly the Falcon 9 rocket.
The booster has etched a number of superlative firsts, from vertical landing and subsequent reuse, to flying into orbit with a record nine first-stage engines. And then there is its cost. At the time of its debut a decade ago, SpaceX offered a basic launch on the Falcon 9 rocket for $50 million. After a few incremental increases, since 2016, SpaceX has listed the base Falcon 9 price at $62 million. This put tremendous pressure on competitors in the satellite launch industry.
Approximately two-thirds of the global launch market is effectively closed to competition because these are national payloads. For example, Russia and other space-faring countries will typically launch their military and science satellites on domestic rockets. Only about one-third of the overall launch market—consisting of satellite constellations, communications and imaging satellites for nations without launch programs, and other payloads—is truly open to competition.
Decades ago, US launch companies ceded this commercial market as they began to focus on winning more lucrative contracts to launch payloads for the US military. By 2006, when Boeing and Lockheed Martin consolidated their rocket businesses into a single company, United Launch Alliance, America essentially captured zero percent of the competitive launch market. Customers in the United States and abroad turned to more economical launchers in Europe, Russia, and elsewhere to reach orbit. Meanwhile, with a monopoly on launching missions for NASA and the US Department of Defense, United Launch Alliance’s prices steadily rose.
The success of the Falcon 9 rocket reversed this trend dramatically. Seeking lower cost delivery of supplies to the International Space Station, NASA invested $396 million in SpaceX from 2006 to 2010 to develop its Cargo Dragon spacecraft, the Falcon 9 rocket, and a launch pad at the Cape. This investment, which precipitated the June 4, 2010 launch from Florida, delivered not just value for NASA, but for the country.
“Because of the investments that NASA has made into SpaceX we now have, the United States of America now has about 70 percent of the commercial launch market,” said the space agency’s administrator, Jim Bridenstine. “That is a big change from 2012 when we had exactly zero percent.”
Snipping the nozzle
Earlier this year, I asked Musk about that late-night ride to the launch pad in June 2010 and the last-minute fix to the Falcon 9 rocket's avionics.
“It seems pretty crazy to me that you launched the next day, and it was like, a perfect launch,” I said.
“I've done crazier things than dry out a radio antenna,” he replied.
In fact, they did said crazier thing on the very next flight of the Falcon 9. SpaceX put its second Falcon 9 rocket on the pad in early December 2010. The purpose of this flight was to test the Dragon capsule in flight and during reentry through Earth’s atmosphere. This mission received a lot of attention because SpaceX cheekily put a wheel of Brouère cheese inside the capsule as a nod to Monty Python’s "Cheese Shop" sketch.
But the real drama, again, involved the Falcon 9 rocket’s second stage. This upper part of the Falcon 9 rocket, which pushes a payload into orbit after the larger first stage falls away, is powered by a single Merlin vacuum engine. The engine has an extended nozzle for optimal thrust above Earth’s atmosphere. It is made from a C-103 niobium alloy, a fairly strong material.
Preparations for the Falcon 9’s second flight had gone smoothly up until the final pre-launch photo inspections a couple of days before the December 8 launch date. But from these photos, SpaceX’s launch team realized they had a serious problem. “There was a tear at the bottom of the skirt,” Musk said. “And I'm like, 'What the hell are we going to do?'”
The crack extended almost one-third up the nozzle. What had happened is this: about one month before the launch, SpaceX received a requirement from NASA to add more gaseous nitrogen to the rocket’s interstage. So technicians ran a 1-inch line into the bottom and blasted the nitrogen in. This flow caused the Merlin engine nozzle to vibrate—and eventually crack.
-
Days before the second launch of a Falcon 9 rocket, Elon Musk called in technician Marty Anderson, seen here rising to the rocket.Tim Buzza
-
The rocket launched on Dec. 8, 2010.
-
That feeling when you put your second Falcon 9 rocket into space.Tim Buzza
-
The launch carried a Dragon demonstration capsule.NASA
-
Also inside? A wheel of cheese.NASA
-
With this launch NASA was certifying the Dragon spacecraft as a cargo delivery vehicle.NASA
-
The rocket climbed above Cape Canaveral Air Force Station.NASA
-
SpaceX rebuilt Space Launch Complex-40 there.NASA
-
The Dragon capsule that launched from Launch Complex-40 at Cape Canaveral Air Force Station aboard a SpaceX Falcon 9 rocket is recovered in the Pacific Ocean about 500 miles west of the coast of Mexico.SpaceX
The rocket could not launch with a cracked nozzle. But replacing this one would be a cumbersome process, requiring the company to accelerate production of a nozzle at its California-based factory, ship it to Florida, and install it on the rocket. This would likely have taken as long as a month.
Musk hated to substantially delay the mission. With this first launch of the Cargo Dragon spacecraft, he knew full well SpaceX stood to make history. No private company had ever launched a spacecraft into orbit before and then safely retrieved it. So he took out his phone and rang up Marty Anderson, one of the company's ace technicians.
"Hey Marty, do you think you can just go and climb in the interstage and cut the bottom six inches off the skirt?” Musk asked.
No joke—Musk wanted Anderson to go into the rocket with a pair of metal shears and trim the bottom of the skirt. This was the solution to a tear in an engine nozzle.
Anderson was game. Hours later, he flew on Musk’s private jet from the company’s factory in California to Florida, got into a lift, and rode a crane up to the interstage. This happened with the rocket standing upright, out on the launch pad. Soon, Anderson had snipped away the skirt at the bottom of the engine.
The shorter engine nozzle would cost SpaceX a small hit on the upper stage’s performance, with a decreased specific impulse. But the bigger worry was that the cut breached an anti-oxidation coating, which could lead to some erosion after ignition. “We figured as long as the rate of erosion is not too fast you'll be OK,” Musk explained.
But Musk did not have the final say. After the fact, SpaceX had to convince its customer, NASA, about the soundness of this solution. Success on this flight would bring SpaceX a big step closer to beginning cargo delivery to the station. Losing the Dragon spacecraft before it could complete its key orbital tests, on the other hand, would be a serious setback for both NASA and the company.
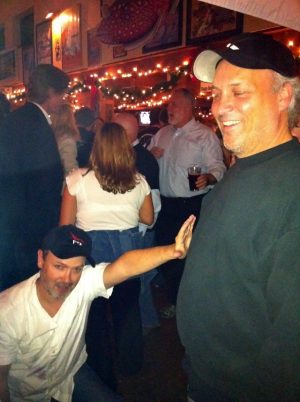
Buzza, the company's longtime launch director, said it was not easy to convince NASA. He and other vice presidents at the company, including Hans Koenigsmann and Tom Mueller, presented their findings to NASA’s leaders in the commercial cargo program, including Mike Horkachuk and Alan Lindenmoyer.
“They could not fathom what we were proposing, and in fact what we had already done by cutting the nozzle off,” Buzza said.
But the SpaceX vice presidents and NASA’s engineers worked the problem together, for about 24 hours straight. At the end of their analysis, they forwarded their work to NASA’s chief of human spaceflight, Bill Gerstenmaier, who had the ultimate authority. “At 2am the night before launch, Elon called me and said that he talked to Gerstenmaier,” Buzza said. “We had the thumbs up to go for launch.”
Shortly before noon the next day, the Falcon 9 rocket lifted off. The launch was successful again, with the trimmed second stage working fine. Three hours later, Dragon and its cheesy comestible returned safely to Earth. That night, the SpaceX team partied hard. They had a working rocket and a spacecraft.
“Quite a record”
The Falcon 9 was not without flaws. On its seventh commercial resupply mission (CRS-7) in June 2015, the booster failed on its way to orbit, destroying the Dragon carrying supplies to the International Space Station. The company lost yet another rocket a little more than a year later, during a static fire test at Cape Canaveral.
Since then, SpaceX has flown the Falcon 9 rocket successfully more than 50 times consecutively. And all along the way, the SpaceX engineers were learning about their booster, ever seeking to improve it.
Most visibly, the company demonstrated reuse of the first stage booster. On its very next mission following the CRS-7 failure, in fact, SpaceX landed a Falcon 9 first stage for the first time. The next April, the company nailed its first drone ship landing. Then, in March 2017, the company successfully re-flew a Falcon 9 first stage for the first time. In the three years since, SpaceX has landed more than 50 rockets and flown the same booster five or more times.
Carissa Christensen, founder of Bryce Space and Technology, an analytics firm, said the reuse of vertically launched and landed rockets had been discussed in the aerospace community for decades. "This was always something that would make a difference, and it was desirable, but it never happened," she said. "Then SpaceX made it happen."
Moreover, she said, the company did this on its own initiative. Typically in spaceflight, a government agency will offer a contract for some type of project and pick a contractor to do the work. Although SpaceX received a substantial amount of NASA funding for cargo and crew delivery to the space station, it got no money for reuse. Instead, Christensen said, the company invested its own funds to clear a "very, very high" technical hurdle that others had aspired to. In return for chancing its own funds on reuse, SpaceX now has the world's only reusable, orbital rocket, and it has just furthered its ability to dominate the commercial satellite market.
-
In April 2016, SpaceX landed a booster on a drone ship for the first time.SpaceX
-
SpaceX founder Elon Musk described the drone ship as a small "postage stamp" out in the ocean.SpaceX
-
Needless to say it got hot when the rocket came down.SpaceX
-
The drone ship, Of Course I Still Love You, is named for the Culture series by Iain M. Banks.SpaceX
-
Here's another view from a different camera on board.SpaceX
-
And it's down. Where's the "wash me" sign?SpaceX
-
The drone ship measures 91 meters by 52 meters.SpaceX
-
The April 2016 landing occurred in relatively calm seas, with a 2 to 3 degree pitch.SpaceX
-
Musk said the rocket could handle double that pitch fairly comfortably and might even be able to accommodate three times as much.SpaceX
-
The landing marked the first time a rocket had ever flown into space and landed on a ship-based platform.SpaceX
-
The company had tried previously on five separate occasions and learned from each failure.SpaceX
-
But practice makes perfect...SpaceX
-
And they stuck the landing.SpaceX
-
The drone ship returned to port a few days later. It could definitely use a scrub, and no doubt it has gotten one.SpaceX
Over the course of the decade, she said, SpaceX has used the Falcon 9 rocket to not only capture the commercial satellite launch market, but NASA's cargo and crew programs, some of its science missions, and, increasingly, military contracts. The Falcon 9 rocket first stage also is the foundation of the Falcon Heavy rocket, the most powerful booster in the world. "SpaceX has really demonstrated that vehicle as being very adaptable," she said. "It has quite a record."
Around the world, companies and countries are struggling to compete. In America, United Launch Alliance is retiring its Atlas and Delta rockets in favor of the more competitive Vulcan booster. Japan's H3 rocket was inspired by a need to reduce prices. Russia is phasing out its storied Proton rocket. Arianespace is retiring the venerable Ariane 5 rocket in favor of a lower cost Ariane 6. It remains to be seen whether any of these boosters can catch up to the Falcon 9, because SpaceX is always moving, Christensen said.
"It's clear that the space industry is on a path toward next-generation launch vehicles," she said. "But SpaceX is 10 years ahead of those next-generation launch vehicles. SpaceX had its first launch of its next-generation launch vehicle 10 years ago." The world of launch, she marveled, has tilted almost beyond recognition from a decade ago. Then, SpaceX was the upstart. Now the Falcon 9 is considered the old, reliable launch vehicle.
Building the future
During the first half of this decade, SpaceX was focused on increasing its flight rate. More launches meant more revenue. And after growing pains, the company succeeded, increasing its flight rate from an average fewer than four launches a year through 2016, to about 20 flights annually of late.
This increasing cadence came even as SpaceX sought to substantially improve the rocket's performance. The company introduced three major upgrades after five launches on the initial Falcon 9 flown a decade ago. Version 1.1 came along in 2013, with larger fuel tanks and a 60-percent improvement in thrust. Falcon 9 Full Thrust followed in 2015, and it featured upgraded Merlin engines and a larger second stage.
Rob Meyerson, who was president of the Blue Origin space company for 15 years, marveled at the gains made between the 1.1 and Full Thrust versions.
"They nearly doubled their performance to Geostationary Transfer Orbit in 18 months," he said. "That is absolutely remarkable. For an industry that prides itself on configuration control and minimizing changes, the amount of change that had to go on inside SpaceX to make all of that happen, and to manage it, is remarkable."
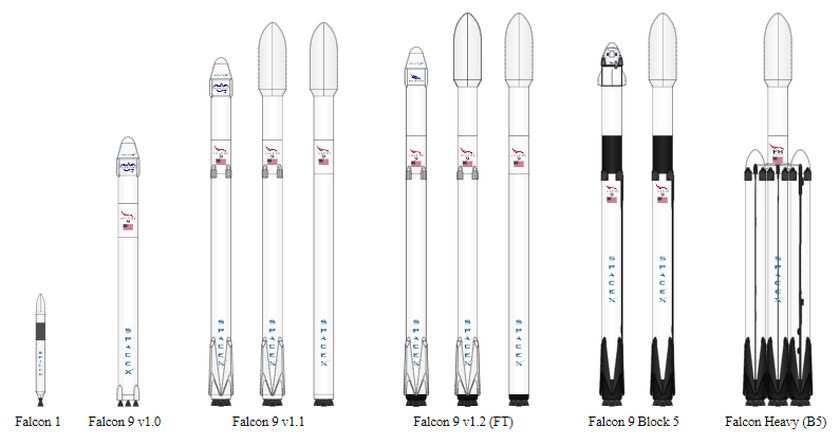
These performance gains were what ultimately enabled Falcon 9 reuse. In May 2018, the company introduced its final major revision to the Falcon 9 rocket, dubbed "Block 5." This optimized the booster for reuse, as only this Block 5 version has ever flown more than twice. All told, the lift capacity of the Falcon 9 rocket increased from 10 tons to low-Earth orbit in 2010, to 22.8 tons in 2018. With this extra performance, SpaceX could set aside fuel for controlled landings and, ultimately, reuse.
Now, much of Elon Musk's focus is on developing his next-generation launch system, Starship. The Falcon 9 is history, and for SpaceX, Starship is the future.
But there would be no Starship without the Falcon 9. With this rocket, Musk proved to NASA and the rest of the world that SpaceX could build world-class rockets. This booster served as a laboratory to push performance and learn difficult lessons about reuse. Now, as the world runs to catch up to the Falcon 9, Musk can afford to look to a future he envisions of low-cost, truly interplanetary travel.
"Sauce" - Google News
June 03, 2020 at 06:20PM
https://ift.tt/2Blmyrh
Forget Dragon, the Falcon 9 rocket is the secret sauce of SpaceX’s success - Ars Technica
"Sauce" - Google News
https://ift.tt/35DSBgW
Shoes Man Tutorial
Pos News Update
Meme Update
Korean Entertainment News
Japan News Update
Bagikan Berita Ini
0 Response to "Forget Dragon, the Falcon 9 rocket is the secret sauce of SpaceX’s success - Ars Technica"
Post a Comment